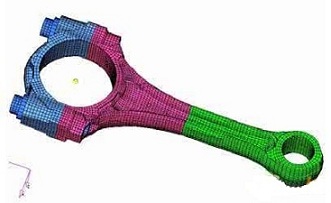
連桿是連接發(fā)動機活塞與曲軸的一個重要零件,在工作中承受拉伸、壓縮和彎曲等交變載荷的作用。隨著柴油機強化程度的不斷提高,連桿承受各類載荷也越來越高,對連桿的強度要求也不斷提高。過去以經(jīng)驗、參考資料和安全系數(shù)法為主的連桿設計方法,連桿尺寸選擇不是過大就是過小,對結(jié)構(gòu)設計的安全性缺乏定量指標。有限元分析法作為一種有效的方法,在連桿的設計、優(yōu)化過程中已經(jīng)得到了廣泛應用。
運用ANSYS軟件對195柴油機的連桿進行了三維有限元分析,得到了連桿的應力分布和強度安全系數(shù)等結(jié)果,并對連桿結(jié)構(gòu)參數(shù)進行了優(yōu)化設計,為連桿的可靠性設計提供了依據(jù)。建立準確、可靠的計算模型是應用有限元法進行分析的重要步驟之一。本研究中的分析對象主要為連桿體,為了節(jié)省分析時間且不影響分析精度,建模時省略了一些不重要的環(huán)節(jié),對連桿模型的大頭端做了簡化處理,忽略了連桿螺栓、軸瓦和襯套和螺栓的預緊力,把連桿體和連桿蓋作為一個整體建模,保留了包括油孔、圓角、倒角、加強筋等幾何特征。
連桿實體模型建立后,將其導入ANSYS軟件中,定義材料屬性,劃分網(wǎng)格,生成有限元模型。本文中我們采用的是10節(jié)點的SOLID92單元,自由網(wǎng)格劃分方式。模型劃分后,共得到17 976個單元,31 861個節(jié)點。
連桿在工作中主要承受從活塞傳遞來的氣缸壓力、活塞和連桿組件的慣性力,兩者隨連桿的往復運動通過連桿大、小頭孔中心的連線周期性的作用在連桿大、小頭孔的內(nèi)表面上,因此連桿在工作期間都處于拉伸、壓縮交替變形狀態(tài)。為了便于用有限元方法對連桿應力、應變情況進行分析,采用了準動態(tài)模擬分析法,分析中只考慮連桿承受最大壓縮力和最大拉伸力的兩種極限載荷工況。
最大拉伸力工況發(fā)生在進氣沖程開始的上止點位置附近,連桿承受的最大拉伸力為活塞組件和連桿計算斷面以上部分的往復慣性力。
最大壓縮力工況發(fā)生在做功沖程開始的上止點位置附近,連桿承受的最大壓縮力為最大爆發(fā)壓力減去此連桿活塞組的慣性力。
大、小頭孔內(nèi)表面處承受的載荷在軸線方向均沿二次拋物線分布,徑向呈余弦分布。最大拉伸工況連桿小頭孔處載荷沿小頭孔圓周方向在120范圍內(nèi)按余弦分布,連桿大頭孔載荷沿大頭孔圓周方向在180范圍內(nèi)按余弦分布。最大壓縮工況連桿大、小頭孔處的載荷均沿各孔的圓周方向在180范圍內(nèi)按余弦分布。
連桿在工作過程中作平面運動,而計算工況是選定兩種極限載荷位置,強度分析中連桿的變形也是自身的相對變形,且連桿兩端負載,故取連桿大小頭孔連線的中間位置截面作為固定約束,限制其剛體位移和轉(zhuǎn)動;連桿受壓工況,在連桿大頭內(nèi)側(cè)上部120處施加徑向約束;連桿受拉工況,則在連桿大頭內(nèi)側(cè)下部120處施加徑向約束。
在工作中,連桿一直承受不對稱循環(huán)應力作用,有必要從疲勞強度的角度來評價連桿的安全問題。為了有效地計算疲勞安全系數(shù),將一個復雜的應力狀態(tài)轉(zhuǎn)化為一個具有相同等效“效應”的單向應力狀態(tài),稱為等效應力,其大小按第四強度理論計算。
優(yōu)化參數(shù)選擇考慮到了以下幾點:①對零件整體質(zhì)量影響較大;②在一定程度上能描述結(jié)構(gòu)外形且相互獨立;③對發(fā)動機整體參數(shù)及其它零部件主要尺寸無影響;①工藝上實現(xiàn)相對容易。我們選擇了8個優(yōu)化參數(shù)。
在進行連桿優(yōu)化設計過程中,為保證連桿設計的可靠性和合理性,必須滿足下列約束條件:
連桿結(jié)構(gòu)的最大拉應力不能超過許用值,連桿的最大壓應力不能超過許用值。連桿大、小端孔的最大收縮量不能超過許用值。連桿結(jié)構(gòu)的疲勞安全系數(shù)不能小于許用值,設計變量應在一定范圍內(nèi)變動,即桿身凹槽則按一定比率隨桿身輪廓變化而變化;在Z平面上,表示桿身的高度,為過渡圓弧在Xz平面的直徑。
專業(yè)從事機械產(chǎn)品設計│有限元分析│強度分析│結(jié)構(gòu)優(yōu)化│技術(shù)服務與解決方案
杭州那泰科技有限公司
本文出自杭州那泰科技有限公司m.0419pingan.com.cn,轉(zhuǎn)載請注明出處和相關(guān)鏈接!